Post Shipment Inspection: Your Ultimate Guide To Supply Chain Assurance
In the intricate world of global trade, the journey of goods from manufacturer to final destination is fraught with potential pitfalls. Even after products leave the factory and pass initial checks, the risk of damage, loss, or non-compliance during transit remains a significant concern. This is precisely where **post shipment inspection** emerges as an indispensable safeguard, offering a critical layer of quality control and assurance long after the products have been dispatched. It's not merely an afterthought but a proactive measure designed to protect your investment, your brand, and your customer relationships in an increasingly complex supply chain environment. Understanding its nuances and implementing effective strategies can mean the difference between seamless operations and costly disputes.
For businesses engaged in international commerce, the stakes are incredibly high. A shipment arriving damaged, incomplete, or not conforming to agreed specifications can lead to significant financial losses, reputational damage, and strained supplier relationships. This guide aims to demystify post shipment inspection, exploring its vital role, the processes involved, and how it contributes to maintaining product integrity and compliance throughout your supply chain. Whether you are a manufacturer, supplier, or logistics professional, learning how to effectively manage this crucial phase is paramount to your success and peace of mind.
Table of Contents
- What is Post Shipment Inspection?
- Why Post Shipment Inspection is Crucial for Your Business
- Key Aspects: What Post Shipment Inspection Covers
- The Indispensable Role of Third-Party Inspection Providers
- Tangible Benefits of Implementing Post Shipment Inspection
- The Process of a Thorough Post Shipment Inspection
- Distinguishing Post Shipment from Pre-Shipment Inspection
- Implementing Effective Post Shipment Inspection Strategies
What is Post Shipment Inspection?
At its core, **post shipment inspection** is a critical quality control process that takes place after goods have been shipped from the supplier's location, typically upon their arrival at the buyer's designated port, warehouse, or distribution center. Unlike pre-shipment inspection, which focuses on verifying product quality and quantity *before* dispatch, post shipment inspection addresses the integrity of the goods *after* they have endured the rigors of transit. This crucial inspection helps address any issues that may arise after the goods have been shipped, ensuring that what was sent is what was received, and that it remains in the expected condition.
- %C3%B6zge Ya%C4%9F%C4%B1z
- What Is A Low Taper Fade
- Gabrielle Anwar Birth Year
- Terrel Williams Boxing
- Where Is Iran Located In The World
The primary objective of this inspection is to provide a final assurance that the products meet the required quality and quantity standards, and conform to the specifications agreed upon in the sales contract. It serves as a vital checkpoint, allowing businesses to verify the condition, quantity, and compliance of goods after shipment. This meticulous process helps identify transit damages, verify compliance, and protect brand reputation, safeguarding against potential losses and ensuring customer satisfaction. Without this final check, businesses are often left vulnerable to unforeseen problems that can emerge during the shipping process, from mishandling to environmental damage. It is a testament to a commitment to quality that extends beyond the factory floor, embracing the entire journey of the product.
Why Post Shipment Inspection is Crucial for Your Business
In the global marketplace, where supply chains span continents and involve multiple touchpoints, the potential for unforeseen issues is ever-present. From rough handling during loading and unloading to environmental factors like temperature fluctuations or humidity, goods are exposed to numerous risks during transit. This is precisely why **post shipment inspection** isn't just an option; it's a necessity for businesses aiming for excellence and sustainability. The consequences of neglecting this final check can be severe, ranging from immediate financial losses to long-term damage to a company's reputation.
Firstly, it acts as a critical safeguard against financial setbacks. Imagine receiving a large order only to discover a significant portion of it is damaged or missing. Without a robust post shipment inspection process, proving liability and claiming compensation can become an arduous, if not impossible, task. By verifying the condition, quantity, and compliance of goods after shipment, businesses are empowered to identify discrepancies early, enabling prompt action for claims against carriers or suppliers. This proactive approach helps businesses avoid costly mistakes that can erode profit margins and strain operational budgets.
- What Nationality Is Katie Miller
- Ben Napiers Marriage Issues
- Sodi Age
- Professional Candid Photography
- Distance Between Iran And Israel Kilometers
Secondly, it is indispensable for maintaining compliance with regulations and upholding quality standards. Different countries and industries have specific import regulations, quality benchmarks, and safety standards that products must meet upon arrival. A comprehensive post shipment inspection ensures that the delivered goods not only conform to the specifications agreed upon in the sales contract but also adhere to all relevant regulatory requirements. This adherence is vital for avoiding legal penalties, customs delays, and potential product recalls, all of which can severely impact a business's operational flow and public image. It underscores a commitment to delivering products that are not only fit for purpose but also legally compliant and safe for consumers.
Finally, and perhaps most importantly, post shipment inspection is a powerful tool for protecting and enhancing brand reputation. In today's interconnected world, a single instance of a customer receiving a damaged or non-compliant product can quickly escalate into widespread negative publicity. Conversely, consistently delivering high-quality, intact products builds trust, fosters customer loyalty, and strengthens a brand's position in the market. By ensuring that only products meeting the highest standards reach the end-user, businesses demonstrate their unwavering commitment to quality and customer satisfaction. This process helps identify transit damages, verify compliance, and protect brand reputation, transforming potential liabilities into opportunities for reinforced customer confidence.
Key Aspects: What Post Shipment Inspection Covers
A comprehensive **post shipment inspection** goes far beyond a cursory glance at incoming goods. It involves a detailed and systematic examination designed to uncover any issues that may have arisen during the transit phase. The scope of this inspection is broad, encompassing various critical elements to provide a complete picture of the shipment's integrity upon arrival. Understanding these key aspects is crucial for any business looking to implement an effective post shipment quality control strategy.
Condition and Quantity Verification
One of the primary objectives of post shipment inspection is to meticulously verify the physical condition of the goods and the accuracy of their quantity against the shipping documents and purchase order. Our experienced inspectors thoroughly assess the condition of goods upon arrival, checking for signs of improper handling, damage, or degradation that could have occurred during transportation. This includes looking for crushed packaging, water damage, signs of tampering, or any visible defects on the products themselves. For instance, if a shipment of electronics shows signs of impact damage on the outer cartons, inspectors will delve deeper to check the integrity of the internal packaging and the devices within. This proactive approach ensures that any transit damages are identified immediately, allowing for timely claims and resolution.
Simultaneously, a precise count of the received items is performed. This involves cross-referencing the actual number of units, cartons, or pallets against the packing list, bill of lading, and sales contract. Discrepancies in quantity, whether shortages or overages, can lead to significant financial implications and logistical headaches. For example, if a textile order is short by 500 meters of fabric, identifying this during post shipment inspection allows the buyer to address the issue with the supplier or carrier before production schedules are impacted. This rigorous verification process helps businesses avoid costly mistakes associated with incorrect quantities, ensuring that what was paid for is precisely what was received.
Compliance and Specification Adherence
Beyond mere physical condition and quantity, **post shipment inspection** also delves deep into ensuring that the delivered goods conform to all agreed-upon specifications and regulatory requirements. This inspection ensures that the delivered goods conform to the specifications agreed upon in the sales contract, offering a final assurance that the products meet the required quality and quantity standards. This aspect is particularly critical for specialized products, components, or goods subject to strict industry standards.
Inspectors will verify that the product's attributes, such as color, size, material, functionality, and labeling, match the exact specifications outlined in the original purchase order and any associated technical drawings or samples. For example, if a batch of furniture components was ordered in a specific wood finish and dimension, the inspection would confirm these details upon arrival. Any deviation, no matter how minor, could render the product unusable or unsellable, leading to significant rework or rejection costs.
Furthermore, compliance with relevant national and international regulations is a non-negotiable aspect. This can include checking for correct safety certifications, environmental compliance marks, proper country-of-origin labeling, and adherence to import restrictions. For instance, toys imported into the EU must meet CE marking requirements, and their absence or incorrect application would be flagged during this inspection. This meticulous check helps prevent costly delays at customs, legal liabilities, and potential market access issues, safeguarding the business from non-compliance penalties. By covering these critical aspects, post shipment inspection provides a comprehensive safety net, ensuring product integrity and compliance in your supply chain.
The Indispensable Role of Third-Party Inspection Providers
While some large corporations might have the internal resources to conduct their own **post shipment inspection**, the complexity and global nature of modern supply chains often necessitate the involvement of independent, third-party inspection providers. This approach offers unparalleled objectivity, expertise, and reach, which are crucial for effective quality assurance. This requires a globally respected testing and certification services provider such as TÜV SÜD to be present throughout the supply chain, ensuring integrity and compliance at every stage.
Third-party agencies bring a level of impartiality that internal teams, no matter how dedicated, cannot always match. Their primary allegiance is to the truth of the inspection, free from any potential internal pressures or biases that might influence a company's own employees. This independence is vital for establishing trust and credibility, especially when disputes arise between buyers and sellers or carriers. For example, if a buyer claims transit damage, an independent inspection report from a reputable firm like TÜV SÜD carries significant weight in arbitration or insurance claims, providing an unbiased assessment of the situation.
Moreover, these providers possess specialized expertise and a global network that most individual businesses lack. They employ experienced inspectors who are trained in various product categories, industry standards, and international regulations. They understand the nuances of different shipping methods and the specific types of damage or non-compliance that can occur. TÜV SÜD, for instance, has a vast network of inspectors and laboratories worldwide, capable of conducting detailed assessments in diverse environments. This global presence means they can be present at the point of arrival, wherever that may be, offering consistent service quality across different regions. They are equipped with the necessary tools and methodologies to thoroughly assess the condition of goods upon arrival, checking for signs of improper handling, and performing detailed compliance checks.
Leveraging a third-party provider also offers significant operational advantages. It reduces the need for businesses to invest in their own extensive inspection infrastructure, training, and personnel, which can be costly and inefficient, particularly for companies with fluctuating import volumes or diverse product portfolios. Instead, businesses can tap into a ready-made, highly skilled workforce on demand. This flexibility and access to specialized knowledge help businesses avoid costly mistakes, ensure compliance with regulations, and maintain quality standards without diverting their core resources. Learn more about how our pre and post shipment services can fortify your supply chain, providing comprehensive solutions from origin to destination.
Tangible Benefits of Implementing Post Shipment Inspection
The decision to invest in **post shipment inspection** is not just about mitigating risks; it's about unlocking a multitude of tangible benefits that contribute directly to a business's bottom line and long-term success. These advantages extend across financial, operational, and reputational domains, making it a strategic imperative for any company involved in global trade.
Firstly, the most immediate and quantifiable benefit is the significant reduction in financial losses. By verifying the condition, quantity, and compliance of goods after shipment, businesses are in a strong position to identify issues like transit damage, shortages, or non-conforming products before they escalate. This early detection allows for prompt action, such as filing claims with insurance providers or carriers, initiating returns, or negotiating adjustments with suppliers. Without this critical checkpoint, businesses might absorb the cost of damaged goods, incur expenses for rework, or face chargebacks from dissatisfied customers, all of which directly impact profitability. This process helps identify transit damages, verify compliance, and protect brand reputation, directly preventing costly financial drains.
Secondly, post shipment inspection plays a pivotal role in ensuring regulatory compliance and avoiding legal complications. In a world of ever-evolving international trade laws and product safety standards, receiving non-compliant goods can lead to severe penalties, including fines, import bans, and even criminal charges. By conducting thorough checks upon arrival, businesses can confirm that products meet all necessary certifications, labeling requirements, and quality benchmarks specific to the destination market. This proactive compliance management prevents costly delays at customs, avoids potential product recalls, and safeguards the company's legal standing, ensuring smooth market entry and distribution.
Thirdly, it significantly enhances customer satisfaction and strengthens brand loyalty. In today's competitive landscape, customer expectations for quality and timely delivery are higher than ever. When customers receive products that are damaged, incomplete, or not as ordered, it leads to frustration, negative reviews, and a loss of trust. By contrast, consistently delivering products that meet or exceed expectations builds a strong reputation for reliability and quality. Post shipment inspection acts as the final gatekeeper, ensuring that only pristine and accurate orders reach the end-user, thereby fostering positive customer experiences and repeat business. This commitment to quality at the final stage reinforces a brand's promise and builds lasting relationships.
Finally, implementing robust post shipment inspection processes contributes to improved supplier relationships and overall supply chain efficiency. When issues are identified early and objectively, it facilitates constructive dialogue with suppliers, enabling them to understand and rectify the root causes of problems. This feedback loop can lead to better manufacturing processes, improved packaging, and more reliable logistics from the supplier's end. Over time, this collaborative approach builds stronger, more transparent partnerships, leading to a more resilient and efficient supply chain for all parties involved. By ensuring product integrity and compliance in your supply chain, post shipment inspection transforms potential liabilities into strategic advantages.
The Process of a Thorough Post Shipment Inspection
Executing an effective **post shipment inspection** requires a systematic approach, combining careful planning with meticulous execution. The process typically involves several key stages, each designed to thoroughly assess the condition, quantity, and compliance of goods upon their arrival. This structured methodology ensures that no critical detail is overlooked, providing a comprehensive report on the shipment's integrity.
Arrival Assessment and Documentation
The process begins immediately upon the arrival of the goods at the designated receiving point, whether it's a port, a warehouse, or a distribution center. The initial step involves a preliminary visual assessment of the external packaging and containers. Inspectors look for any obvious signs of damage, such as crushed cartons, punctures, water stains, or evidence of tampering. This initial check is crucial for identifying potential issues that may warrant a more in-depth examination. Any visible damage to the outer packaging is documented with photographs and detailed notes, which are vital for insurance claims or disputes with carriers.
Simultaneously, all accompanying shipping documents are meticulously reviewed. This includes the bill of lading, packing list, commercial invoice, and any certificates of origin or compliance. The information on these documents is cross-referenced with the actual shipment to ensure consistency. Discrepancies in container numbers, seal numbers, or gross weights are immediately flagged. This documentation phase is critical for establishing a clear chain of custody and verifying that the received shipment matches the expected consignment. Our experienced inspectors thoroughly assess the condition of goods upon arrival, checking for signs of improper handling, and meticulously documenting every observation.
Detailed Examination and Reporting
Following the initial assessment, a more detailed and systematic examination of the goods commences. This involves unpacking a representative sample of the goods, or in some cases, the entire shipment, depending on the nature of the products and the client's requirements. During this phase, inspectors perform a precise count of the items to verify the quantity against the packing list and purchase order. They also conduct a thorough visual inspection of individual products for any defects, damage, or non-conformities that may have occurred during transit. This could include scratches, dents, breakages, or functional issues. For certain products, specific tests may be performed to ensure functionality or adherence to technical specifications.
Crucially, this detailed examination also verifies compliance with product specifications and regulatory standards. Inspectors confirm that product attributes like color, size, material, labeling, and markings match the agreed-upon criteria. They also check for the presence of required certifications (e.g., CE, FCC, RoHS) and ensure that all necessary warning labels or instructions are present and correctly applied. Any deviations or issues discovered during this phase are meticulously documented, often with photographic evidence, and detailed descriptions of the non-conformity. This inspection ensures that the delivered goods conform to the specifications agreed upon in the sales contract, offering a final assurance that the products meet the required quality and quantity standards.
The culmination of the **post shipment inspection** process is the generation of a comprehensive inspection report. This report serves as an official record of the findings, including a summary of the inspection scope, methodologies used, detailed observations, photographic evidence of any defects or damages, and a clear conclusion regarding the shipment's conformity. This report is an invaluable tool for decision-making, allowing businesses to accept the shipment, initiate claims, negotiate with suppliers, or take corrective actions as needed. It provides the objective data required to address any issues that may arise after the goods have been shipped, safeguarding business interests and maintaining supply chain integrity.
Distinguishing Post Shipment from Pre-Shipment Inspection
While both **post shipment inspection** and pre-shipment inspection (PSI) are vital components of a robust quality control strategy, they serve distinct purposes and occur at different stages of the supply chain. Understanding these differences is crucial for implementing a comprehensive quality assurance program. Pre-shipment inspection is part of quality practice you must undertake when importing from China or any other country, focusing on preventing issues before they even leave the factory.
Pre-Shipment Inspection (PSI), as its name suggests, is a quality control process designed to ensure products meet specific standards and requirements *before* shipment. It is a detailed, comprehensive inspection conducted by a third-party inspection agency to confirm the quality, quantity, and compliance of goods while they are still at the manufacturer's or supplier's facility. This process involves thoroughly checking items to confirm that they match the buyer's requirements, helping prevent costly mistakes and delays. For example, TÜV SÜD prüft als unabhängige Stelle vor der Verladung der Ware, ob diese den Vorgaben des Käufers entspricht. Untersucht werden dabei zum Beispiel Vollständigkeit, Qualität und Defekte. This ensures that only goods meeting the buyer's specifications are loaded onto the vessel or plane, catching potential problems at the source.
In contrast, **post shipment inspection** occurs *after* the goods have been dispatched and typically upon their arrival at the buyer's destination. Its primary focus shifts from preventing initial quality issues to verifying the integrity of the goods after they have endured the stresses of transit. This crucial inspection helps address any issues that may arise after the goods have been shipped, such as damage incurred during handling, transportation, or customs clearance. While PSI aims to prevent non-conforming goods from leaving the factory, post shipment inspection aims to identify and address any problems that develop during the journey, ensuring that the delivered goods conform to the specifications agreed upon in the sales contract upon arrival.
Think of it this way: PSI is like the final quality check before a product leaves the assembly line, ensuring it's perfect before it's packaged. Post shipment inspection is the check performed when the package arrives at your doorstep, ensuring it wasn't damaged or altered during delivery. Both are essential, but they tackle different sets of risks. While PSI prevents the shipment of faulty goods, post shipment inspection safeguards against the perils of logistics. Many businesses learn how our pre and post shipment services provide a complete quality assurance solution, covering every stage from manufacturing to final delivery, offering peace of mind throughout the entire supply chain.
Implementing Effective Post Shipment Inspection Strategies
To truly leverage the benefits of **post shipment inspection**, businesses must move beyond reactive checks and implement proactive, well-defined strategies. An effective strategy integrates inspection into the broader supply chain management framework, ensuring consistency, efficiency, and maximum impact. Explore our guide to effective shipment inspection, providing detailed steps for manufacturers, suppliers, and logistics professionals, and learn how to ensure product integrity and compliance in your supply chain.
Firstly, defining clear and comprehensive inspection criteria is paramount. This involves establishing detailed checklists that specify what needs to be inspected, the acceptable quality limits (AQLs), and the methods for evaluation. These criteria should be based on the sales contract, product specifications, industry standards, and relevant regulatory requirements. For example, if importing delicate glassware, the criteria would include specific packaging integrity checks, visual inspection for chips or cracks, and perhaps a drop test simulation for a sample. Clear criteria ensure objectivity and consistency across all inspections, regardless of who performs them.
Secondly, choosing the right inspection partner is critical. As discussed, independent third-party providers like TÜV SÜD offer expertise, impartiality, and global reach. When selecting a partner, consider their industry experience, accreditations, geographical coverage, and reporting capabilities. A reliable partner will not only conduct the inspection but also provide detailed, actionable reports that facilitate decision-making and claims processes. This requires a globally respected testing and certification services provider such as TÜV SÜD to be present throughout the supply chain, offering unparalleled assurance.
Thirdly, integrating inspection results into a continuous improvement loop is vital. Post shipment inspection should not be a one-off event but rather a source of valuable data that informs future purchasing and logistics decisions. Analyzing recurring issues—whether they are consistent transit damages, persistent quantity discrepancies, or specific product defects—can help identify weaknesses in packaging, carrier performance, or even supplier quality control. This feedback loop allows businesses to work collaboratively with suppliers and logistics partners to implement corrective actions, leading to long-term improvements in product quality and supply chain efficiency. For instance, if a specific type of product consistently arrives with impact damage, it might indicate a need for stronger packaging materials or a different shipping method.
Finally, technology plays an increasingly important role in optimizing post shipment inspection processes. Digital platforms can streamline scheduling, data collection, and reporting, providing real-time visibility into inspection results. Mobile applications allow inspectors to capture high-resolution photos and videos, log observations, and generate reports directly from the inspection site, reducing errors and accelerating communication. Predictive analytics, based on historical inspection data, can even help identify high-risk shipments or routes, allowing businesses to allocate inspection resources more strategically. By embracing these strategies, businesses can transform post shipment inspection from a mere cost center into a powerful tool for risk mitigation, quality assurance, and competitive advantage in the global marketplace. This crucial inspection helps address any issues that may arise after the goods have been shipped, ensuring product integrity and compliance in your supply chain.
Conclusion
In the dynamic and often unpredictable landscape of global commerce, **post shipment inspection** stands as a non-negotiable pillar of supply chain integrity. It is the final, yet profoundly critical, checkpoint that safeguards your investments, protects your brand's reputation, and ensures the ultimate satisfaction of your customers. From meticulously verifying the condition and quantity of goods upon arrival to ensuring their compliance with stringent specifications and regulations, this process is indispensable for navigating the complexities of international trade.
By embracing robust post shipment inspection strategies, ideally with the support of independent and globally respected third-party providers like TÜV SÜD, businesses can proactively identify and address issues that arise during transit. This not only helps avoid costly mistakes and mitigate financial losses but also fosters stronger relationships with suppliers and enhances overall operational efficiency. It's about building a supply chain that is not only resilient but also consistently delivers on its promise of quality and reliability.
We hope this comprehensive guide has illuminated the vital importance of post shipment inspection and provided you with actionable insights to strengthen your own quality control processes. What are your experiences with post shipment inspections? Share your thoughts and questions in the comments below, or feel free to share this article with colleagues who might benefit from these insights. For more detailed information on ensuring product integrity and compliance, explore our other guides on effective supply chain management and quality assurance.
- Stephen Blosil
- Mm2 Values Trading
- Iran Sunni
- Is Dr David Jeremiah Still Alive
- Iran To Israel Map Distance
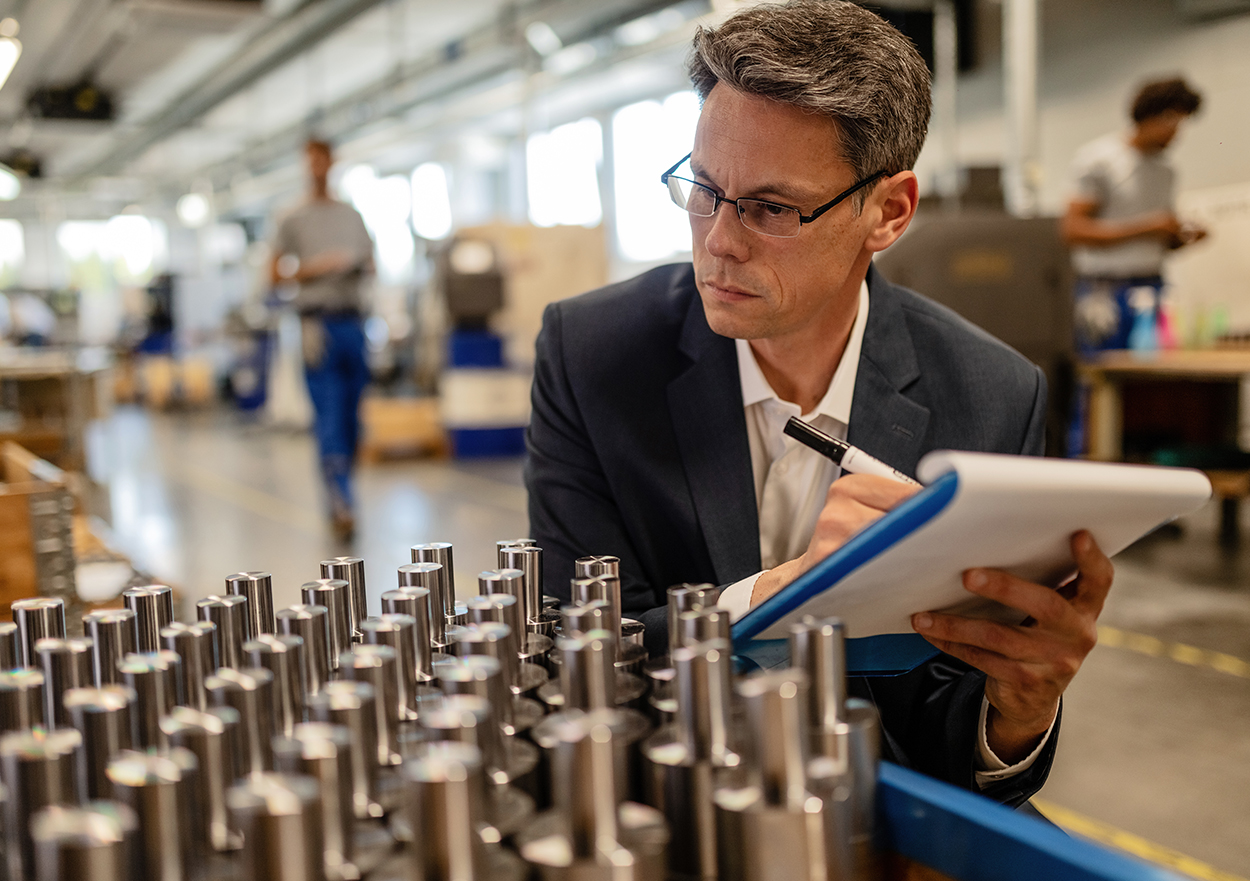
Pre Shipment Inspection (PSI) Service & Third Party Company
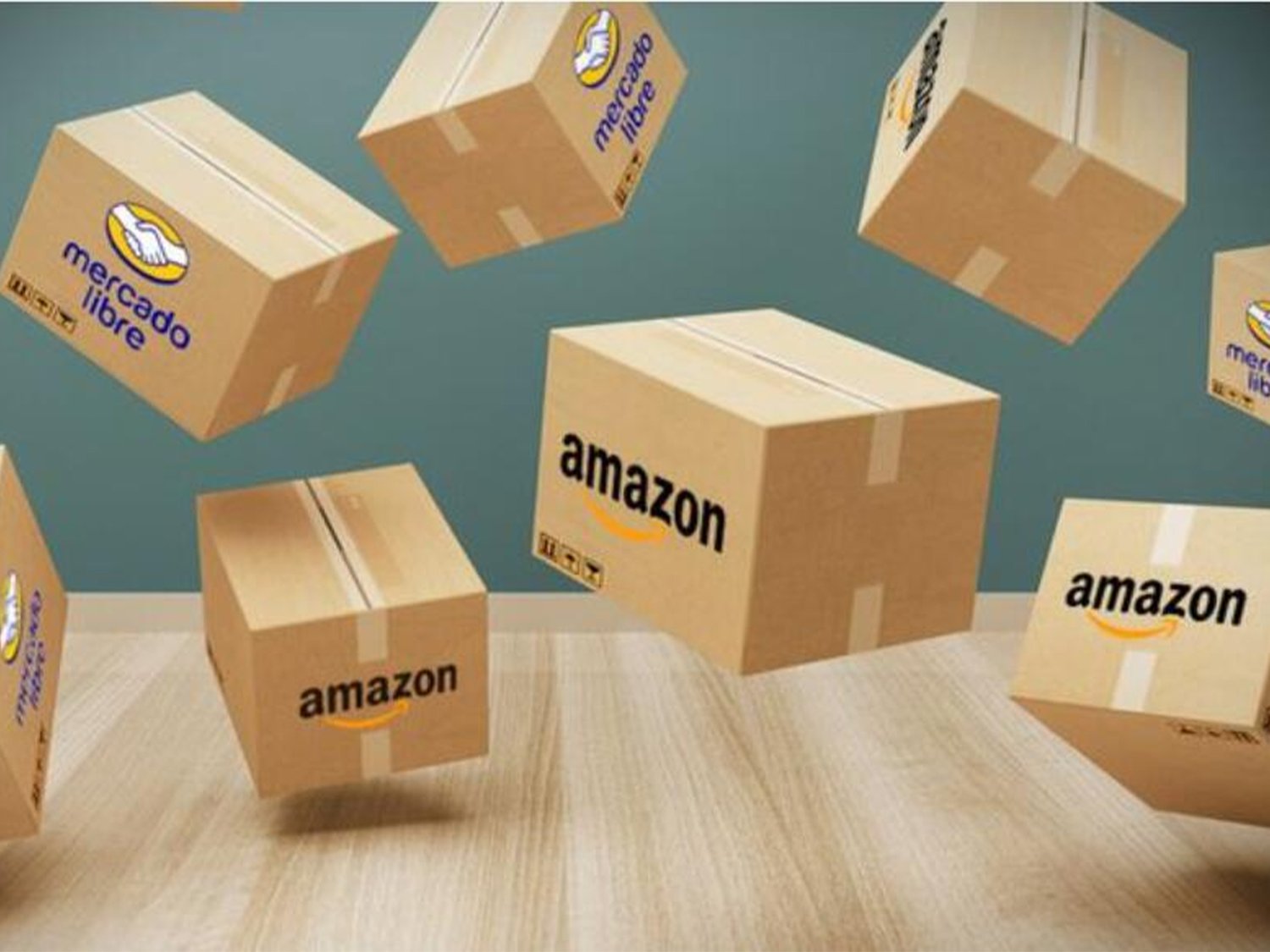
Roy-Inspection
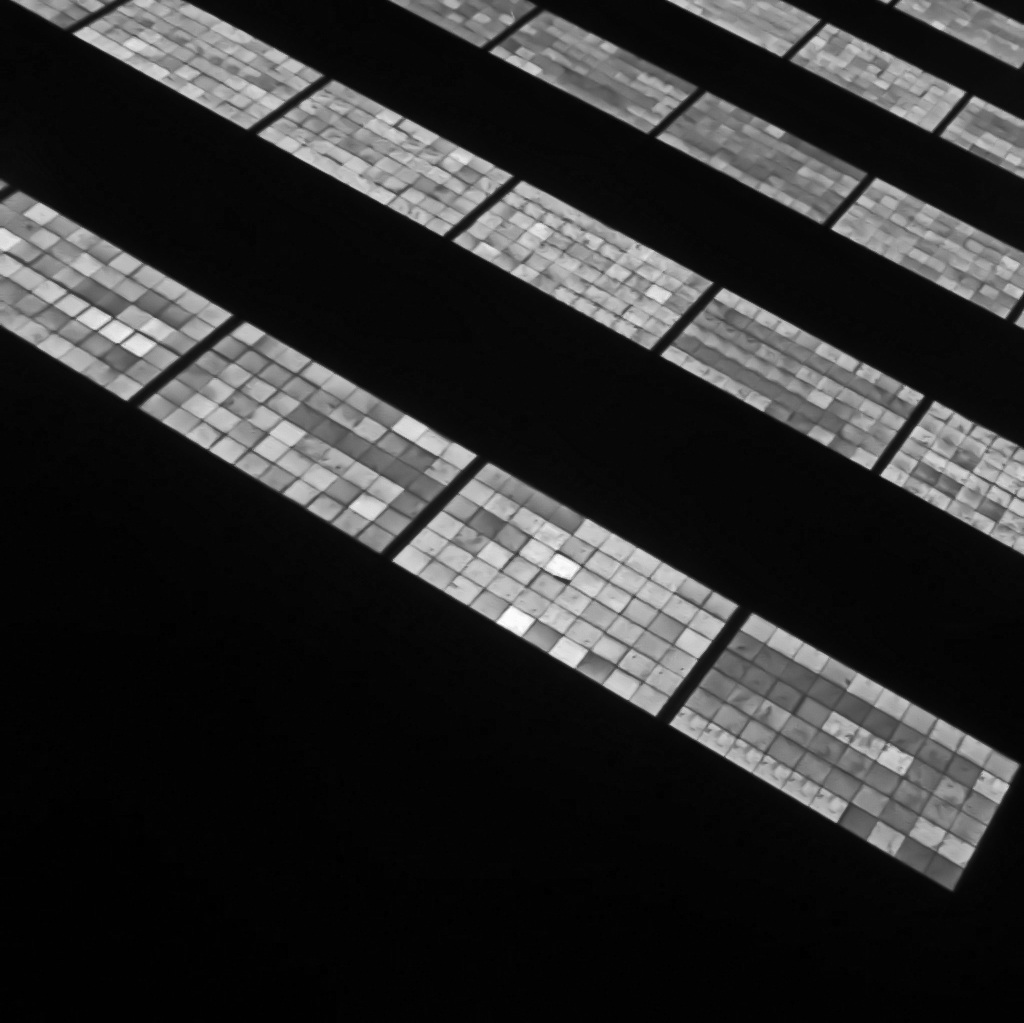
Storage-Post shipment - EL Inspection | Solified